drive.web … configures, connects & controls …
drive.web Overview
drive.web
is an entirely new Internet accessible distributed control technology for machine or process controls.It uses TCP/IP over Ethernet to provide robust connectivity between drives, remote i/o, PLCs, operator stations and SCADA systems.
It incorporates a powerful library of drive control function blocks for a wide range of applications such as PIDs, winder controls, position controls, drive coordination, arithmetic, logic, etc.
It is infinitely scaleable and the distributed control concept ensures that it is cost effective for systems of any size or complexity.
drive.web
provides a completely homogeneous and seamless environment for control systems.drive.web Elements
The drive.web technology consists of four basic elements, or product groups...
Full featured, programmable controllers that provide i/o, communication gateways and distributed control over Ethernet.
Tiny, full featured, programmable controllers that can easily be embedded in devices such as drives, controllers, HMIs, sensors, etc., to provide "smarts," communication gateways and distributed control over Ethernet.
Smart touch screen technology.
Smart HMIs with machine graphics and operator interface. Also runs on iOS, Windows, Mac OS X, and Linux.
A multi-user tool that provides everything you need to configure devices (drives, controllers, HMIs, etc.), design systems, perform diagnostics, create system documentation, and acquire and analyze system data.
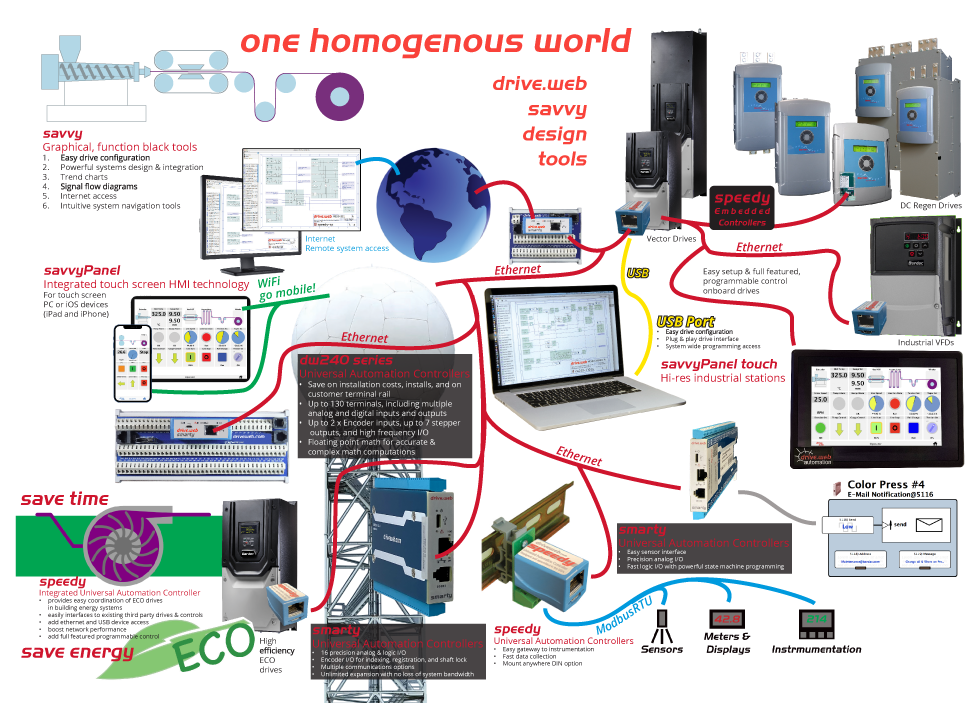
drive.web Connectivity
- drive.web devices (speedys & smartys) connect peer to peer over Ethernet for a completely homogeneous control environment.
- drive.web devices provide full featured programmable control functions.
- There is no limit to system size or complexity.
- ALL system configuration data and touchscreen display information is stored in the drive.web devices - everything!
- Every facet of your system is easily accessible from anywhere.
drive.web Key Features
Online or offline design
of drive systems using the intelligent, intuitive savvy software tools.Graphical Signal Flow Diagram
option provides clear, intuitive system views and documentation.Internet access
to drives and systems for remote configuration, monitoring, diagnostics and training.Any size or complexity
of system supported.Low cost
full-featured Distributed Control capability.Multiple users
from any location can have concurrent real-time access to drives and systems.Libraries of software blocks
such as winder controls, PID controls, position controls, drive synchronization, arithmetic, logic, etc., are used to build system functions of unlimited complexity.Unlimited bandwidth
even with very large networks of drives and controls.Industry standard TCP/IP over Ethernet
is used to provide networking of drives and controls.Platform independent savvy software tools
run on any computer OS that supports Java.Automated software updates
are provided from driveweb.com.Deterministic connections
provide high performance links between drives, PLCs, Operator Stations, SCADA computers and other control products.“Drag & drop” technique
makes easy connections between drives, control devices, and software function block parameters.“Dock” feature
enables users to easily select key monitoring, control and connection points in a large system and “dock” them in convenient windows which can be saved. The “dock” concept aids the organization and documentation of complex systems.Powerful navigation
capability enables users to drill down into detail layers in drives and system processors and to search, jump and browse anywhere in the system for easy visual system comprehension.“Trend” window
enables parameter values to be tracked graphically over time.VPN (Virtual Private Networking)
for secure Internet connectivity is supported in addition to direct Internet addressing.Password protection
is provided for drives and devices as well as the savvy tools.Feature sets
in savvy provide different user levels for Admin, Engineer, Operate and View.ModbusTCP/IP
direct interface over Ethernet.Modbus RTU
on RS485 ports provide low cost for interface to drives, Operator Stations, PLCs, etc.
Contact
Address: 40 Log Canoe Circle
Stevensville, MD 21666
Phone: (410) 604-3400
Toll Free: 1-888-667-7333
(1-888-ON SPEED)
Fax: 410-604-3500
email: info@bardac.com
For emergency after hours phone support call: (410) 604-3535 (payable at time of service with a credit card)